Far from being a futuristic vision, digital twins are now core components of smart factory ecosystems. These ecosystems aim to elevate operational agility, predictive capacity, and cross-functional collaboration, helping companies stay resilient in the face of global supply chain pressures, labor variability, and increasingly stringent sustainability targets.
The global digital twin market, valued at over $24.4 billion in 2025, is forecasted to exceed $259 billion by 2032, growing at a remarkable CAGR of 40.1% (Fortune Business Insights – Digital Twin Market 2025). In manufacturing alone, the market is worth $6 billion this year, making it one of the top three verticals driving this growth (Statista – Digital Twin Market by Industry).
With digital maturity rising across automotive, electronics, and heavy industry sectors, smart factories are rapidly evolving from isolated pilot programs into integrated operational backbones.
One of the most widely referenced implementations is BMW’s digital twin of its Regensburg plant, built on NVIDIA’s Omniverse platform, which enables real-time 3D simulation and planning. Every production detail — from robotic movements to supply chain flow — is virtually modeled to identify and test optimizations before deployment. This has reduced downtime and accelerated AI-driven automation training dramatically (WIRED – BMW’s Virtual Factory).
Similarly, Shanghai Automobile Gear Works, in collaboration with GE Digital, deployed a digital twin-based system using Proficy Plant Applications. The results were concrete: a 20% improvement in equipment utilization, 30% drop in inventory, and 40% reduction in inspection costs — achieved by using a “process digital twin” for real-time analysis and coordination (GE Digital via Wikipedia – GE Digital Case Study).
These use cases illustrate a common truth: digital twins thrive when data and decisions move fluidly across the organization. In this sense, digital twins are not merely a tech deployment, they’re a collaboration framework. Maintenance, production, planning, and quality teams all rely on a unified model of operations that keeps everyone working from the same reality.
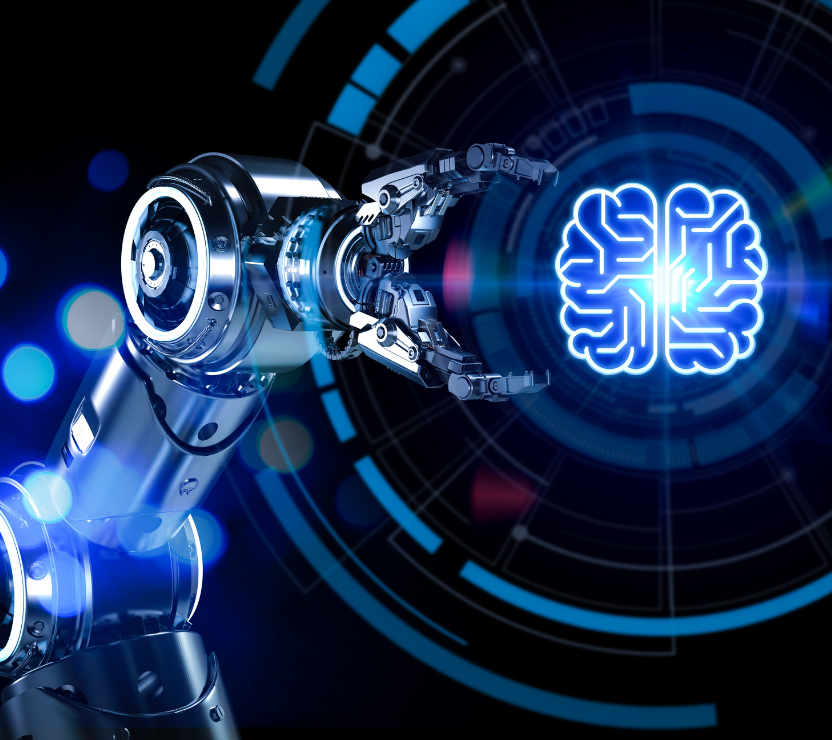
.png)
Digital twins are the heartbeat of smart factories—bridging the physical and digital to drive precision, agility, and innovation in real time.
Top Digital Twin Trends in 2025
As of March 2025, digital twin technologies are evolving rapidly. Here are the five most notable trends:
AI-Enhanced Digital Twins
- Digital twins are increasingly being powered by machine learning algorithms to simulate behavior, detect anomalies, and suggest optimizations. These "intelligent twins" are proactive, not just descriptive. (McKinsey – Digital Twins in Manufacturing).
Edge-Enabled Processing
- Edge computing is enabling digital twins to function closer to the machines — reducing latency and improving response times in real-world environments. (IoT Analytics – Digital Twin Market Trends 2025).
Twin-as-a-Service (TaaS)
- Platforms are now offering digital twins on a subscription model, reducing entry barriers for mid-sized manufacturers looking for scalable deployments. (Gartner & Deloitte via Industry Reports).
Sustainability Integration
- Digital twins are being used to model emissions, energy usage, and material flows, contributing to corporate net-zero goals and ESG metrics. (Fortune Business Insights).
Cyber-Physical Training Systems
- Advanced digital twins are enabling AR/VR-enabled workforce training, where technicians interact with virtual machinery under real-world parameters. (IEEE & Microsoft Manufacturing Cloud Use Cases).
Collaborative Fabric of Smart Factories
The most significant operational benefit of digital twins is not just efficiency, it’s alignment. When every stakeholder, from shop floor technicians to plant heads , operates with shared visibility, the decision-making cycle compresses, and the system becomes more resilient.
In North America, the digital twin market is expected to grow beyond $46 billion by 2031, particularly driven by the integration of AR/VR and AI for collaboration and diagnostics. (Globe Newswire – North America Digital Twin Forecast 2025).
In India, support through SAMARTH Udyog, PLI schemes, and Digital MSME programs is accelerating the adoption of digital twins, especially in auto components, electronics, and mid-sized export-driven factories.
Despite progress, adoption barriers persist, siloed systems, legacy infrastructure, and lack of data readiness. Yet, organizations that prioritize cross-functional design and integration-first architectures are seeing early success.
Conclusion: Smarter Systems, Stronger Teams
Digital twins are no longer optional innovation experiments, they’re fast becoming core infrastructure in smart manufacturing. By mirroring the real-time state of machines, materials, and people, they unlock the ability to not just observe, but orchestrate operations with precision.
As factories look beyond isolated automation and toward holistic performance, the question will not be “Do we have the tools?” but “Are we working in sync with what those tools can see?”
That is the difference between having data and having operational intelligence.
And in 2025, intelligence is no longer about speed.
It’s about shared insight, proactive decisions, and systems that learn — together.